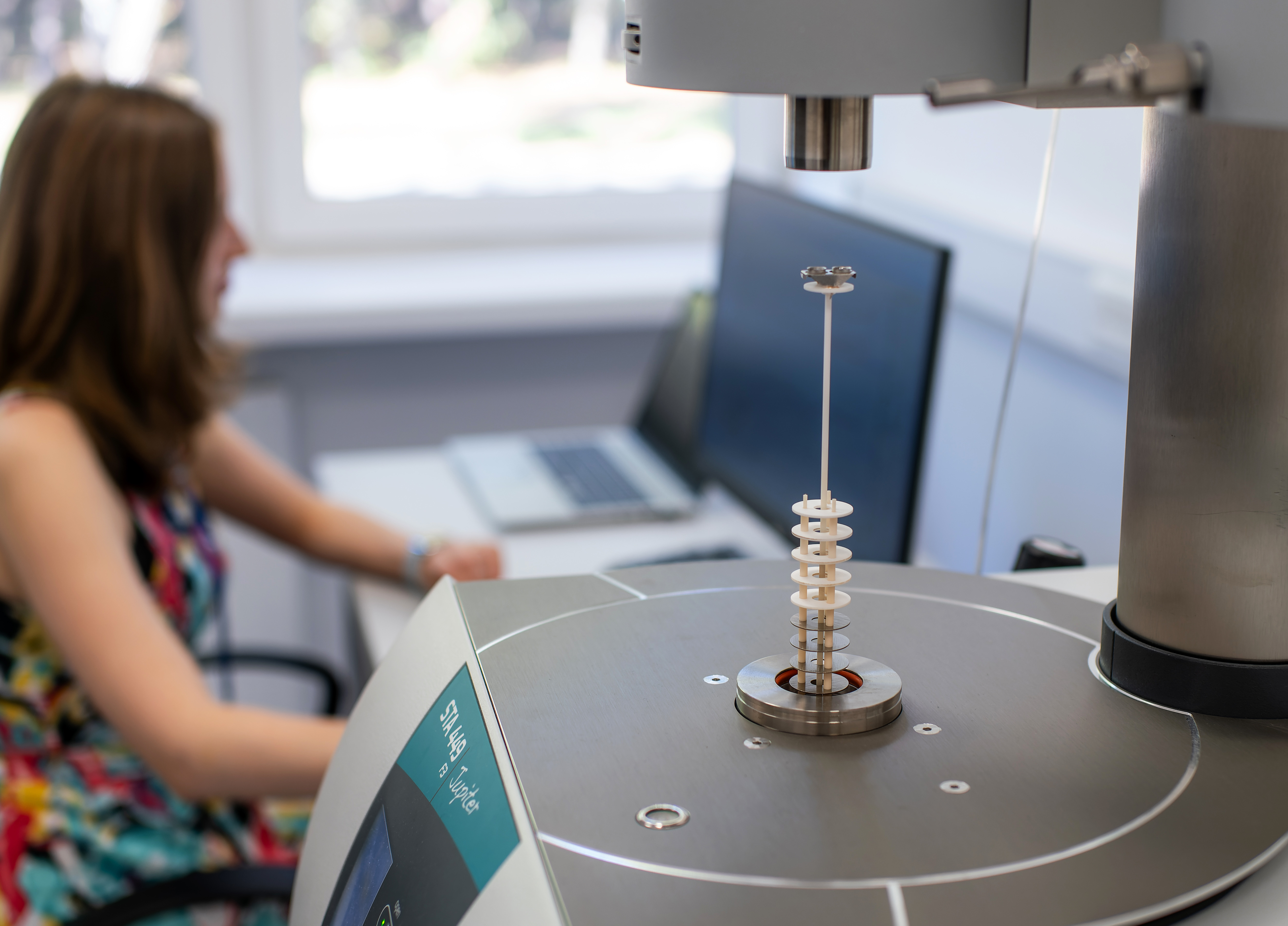
NCBJ Materials Research Laboratory prepared to test the construction materials of the HTGR reactor
28-12-2023
Scientists and Engineers of the NCBJ Materials Research Laboratory specialize in analyzes of mechanical, structural and thermal properties and non-destructive tests of modern materials intended for use in Generation IV nuclear reactors. The recently completed modernization of the Laboratory will allow for testing and certification of materials that will be used to construct the first Polish high-temperature gas-cooled reactor – HTGR.
Developing new energy generation technologies requires specialized engineering knowledge and excellent knowledge of the functional properties of construction materials, because the operational safety of the energy installation largely depends on their selection and subsequent operation. This applies in particular to nuclear installations, where the safety aspect is extremely important and very strictly observed. Currently used research methods and numerical tools allow for precise determination of the properties of a given material. Research can be carried out at the scale of individual atoms and even the interactions between them. Understanding these fundamental interactions is essential to assess and predict the behavior of complete structural elements in a completed nuclear installation. This type of work is the specialty of scientists from the Materials Research Laboratory (LBM) of NCBJ, where the modernization of research infrastructure has just been completed. It opens new possibilities for analyzes and tests of construction materials intended for use in the construction of new generation high-temperature nuclear reactors (High Temperature Gas-cooled Reactor, HTGR).
As the name suggests, HTGR means, first of all, a very high operating temperature, reaching up to 950°C, depending on the design. Moreover, the materials used to build this reactor must be resistant to high pressure and ionizing radiation. Therefore, materials for the construction of this type of reactors must be characterized by unique mechanical and structural properties. To determine whether a given material can work in a given environment, reliable tests must be carried out in conditions similar to those prevailing during its operation. Non-standard conditions should also be taken into account, e.g. emergency states of a nuclear installation, when there is a rapid increase in temperature and pressure.
The way to conduct this type of research is opened by some of the new equipment installed at LBM, including: a high-temperature vacuum furnace designed to simulate the effect of temperature, a high-temperature dilatometer and devices for determining the diffusivity and thermal conductivity of materials. The new devices allow testing of materials at temperatures up to 1250°C in an atmosphere of water vapor or inert gas. LBM laboratories have also been equipped with equipment for destructive and non-destructive material testing, e.g. a portable video borescope, an electro-discharge machine for precise cutting of samples, and a modern mass spectrometer with an inductively coupled plasma system coupled with laser ablation (LA-ICP-MS). This device is intended for very accurate testing of the chemical composition of steel and metal alloys, but it can also be used to determine the chemical composition of graphite – the material from which the elements of the HTGR reactor core will be made.
In the LBM laboratory, the possibilities of conducting in-situ strength tests of materials at temperatures up to 1000°C have also been significantly expanded. In addition to using existing hardness and impact analysis infrastructure, scientists can check the structural properties of materials thanks to a new X-ray diffraction (XRD) and Raman spectroscopy system. "The set of devices we have, supported by detailed structural and phase analysis, allows us to understand the mechanisms responsible for the creation of radiation defects, their migration and interactions not only with each other, but above all with other components of the material's microstructure", describes dr. hab. engineer Łukasz Kurpaska prof. NCBJ, manager of LBM. “This contributes to a better understanding of the behavior of materials in the operating environment of a nuclear reactor, and thus the possibility of accurately estimating their so-called time of life.”
The newly equipped laboratory rooms are also accredited by PCA in the field of mechanical, non-destructive and structural testing, thanks to which the LBM Laboratory is authorized to conduct accredited tests in accordance with international standards for certification of materials and research methods (e.g. ISO, ASTM or BS), among others. for the needs of HTGR technology. This creates new opportunities for cooperation with industry or other research centers in Poland and abroad.
"Thanks to the new research and measurement devices, the Laboratory can perform non-destructive tests, including visual and ultrasonic tests, as well as destructive tests of materials and their welded joints, e.g. macro- and microscopic metallographic analyses, mechanical tests, or assessment of the fracture mechanics of materials and hardness and impact resistance," says dr. hab. engineer Jarosław Jasiński prof. NCBJ with LBM. “In addition, LBM scientists can perform very accurate analyzes of the chemical and phase composition of materials, including: using spectroscopic methods – OES, Raman and mass ICP-MS spectroscopy. Important research aimed at industrial cooperation also includes thermal research, which allows, among other things, to determine the conductivity and thermal expansion of materials as well as the phase transformations occurring in materials during their operation at high temperatures.
Based on the above research capabilities, the LBM Laboratory has already carried out numerous works for scientific and industrial units from the conventional and nuclear energy sectors and many other sectors of the economy. Current work concerns, among others, non-destructive testing of pipe elements intended for the construction of a nuclear reactor cooling system, as well as the assessment of the causes of reduced operational durability of tools used in the automotive industry, and testing of welded joints of ferritic-martensitic ODS steels reinforced with oxide particles, intended for the construction of Generation IV reactors..
It is expected that the purchased infrastructure will enable the implementation of research that will constitute a significant contribution to the commercialization of safe and reliable energy installations, including, above all, Generation IV reactors, which will significantly contribute to the decarbonization of the economy and ensure constant and competitively priced energy production costs. The HTGR project, managed by the National Center for Nuclear Research, is implemented under the agreement of the Minister of Education and Science with the National Center for Nuclear Research of May 12, 2021 on the establishment of a project called "Technical description of a research high-temperature gas-cooled nuclear reactor (High Temperature Gas Cooled Reactor, HTGR)", contract no. 1/HTGR/2021/14.